Printing method of cosmetic plastic bottle packaging pattern and text
1.Silk Screen Printing
-
Definition
Screen printing refers to screen printing with pictures and texts by using screen as the plate base and photosensitive plate making method. When printing on the plastic bottles or containers, the ink is poured into one end of screen printing plate, and the scraper is used to exert certain pressure on the ink part of screen printing plate. At the same time, the ink moves uniformly towards the other end of screen printing plate, and the scraper is squeezed from the mesh of the graphic part to the substrate during the movement.
-
Advantage
Strong stereoscopic sense; strong light resistance. See the silkscreen printing example in the picture as below, the plastic bottles and vial are decorated with silkscreen printing
-
Shortcoming
Only 1-2 color can be printed at a time.
2. Labeling
-
Definition
Complete presentation of complex multi-color labels. Check the example in the picture as below:
-
Advantage
Complete presentation of complex multi-color labels.
-
Shortcoming
Easy to wrinkle.
3.Gold Stamping
-
Definition
Gold stamping is to heat the metal plate, foil, and stamp the gold characters or patterns on the surface of plastic bottles.
-
Advantage
Clear and beautiful patterns;Bright colours;Wear-resisting. See the example as below, the colored plastic bottles stamped with gold color.
-
Shortcoming
Imprints not suitable for hot stamping with rough or matt surfaces.
4.Thermal Transfer Printing
-
Definition
Thermal transfer printing is divided into two parts:transfer film printing and transfer processing. Transfer film printing uses dot printing (resolution up to 300 dpi) to pre-print the pattern on the surface of the film. The printed pattern is rich in layers, bright in color,changeable, small in color difference, good in reproduction, which can meet the requirements of the designer and is suitable for mass production.
-
Advantage
In line with green printing standards, no environmental pollution. Check the example as below picture, the plastic containers decorated with thermal transfer printing.
-
Shortcoming
Poor adhesion,generally need to spray a protective film;Relatively poor gas permeability.
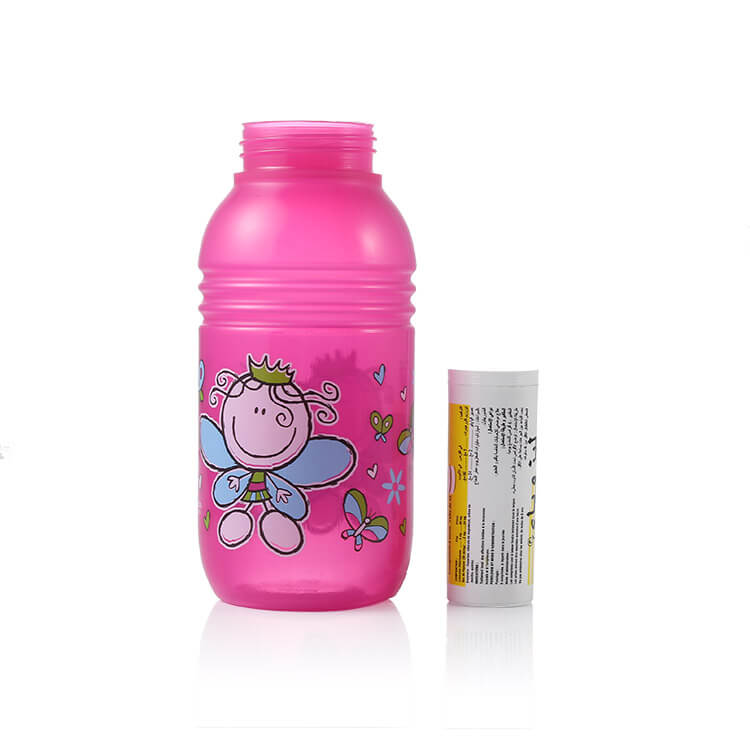
5.Shrink Sleeve
-
Definition
The shrink sleeve label is a film label printed on a plastic film or a plastic tube with a special ink. During the labeling process, when heated (about 70 ° C), the shrink label will quickly follow the outer contour of the container , then shrinking and sticking to the surface of the container.
-
Advantage
Shirk sleeve packaign could provide more wonderful designs and save the costs. They can packing general method to special-shaped product and 360 degree all round branding and messaging on your packaging containers. See the case as below picture, the plastic bottles decorated with shrink sleeve
-
Shortcoming
Required shrinkage ratio of the graphic image, shrink film and ink. The printability of most heat shrinkable films is not very good and requires pre-press pretreatment.
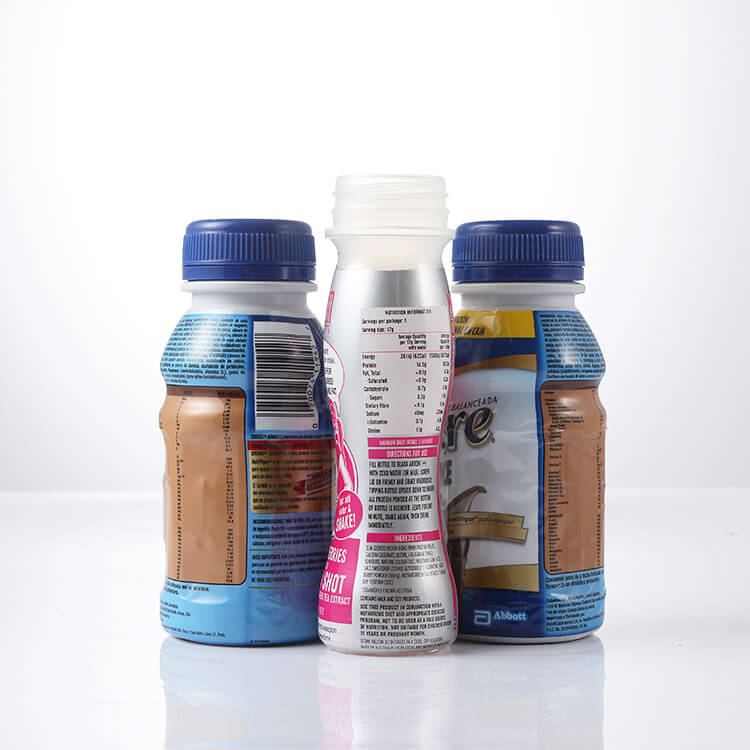
6.Pad Printing
-
Definition
Gravure plate of steel (or copper, thermoplastic) is used for transfer printing. Surface transfer head made of silicone rubber material is used to dip the ink on gravure into the surface of transfer head, andt then press on the surface of the desired object to print text, patterns, etc.
-
Advantage
Can be printed on irregular surface,it has obvious advantages in printing on small area, concave and convex products. See the pad printing example on the picture on the right, the logo printed on the surface of a round ice cream bowl, which manufactured by Sanle - a professional bottle and label manufacturer.
-
Shortcoming
Shortcoming:Printing area is limited by rubber head and steel plate, and large area products can not be printed.
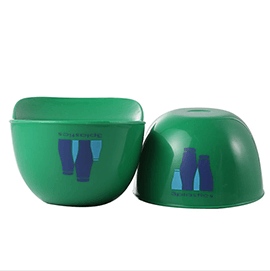
Sinowoo has offers almost any material finish which is technically possible, stretching boundaries to explore new techniques.Here is a selection of some of the options available.